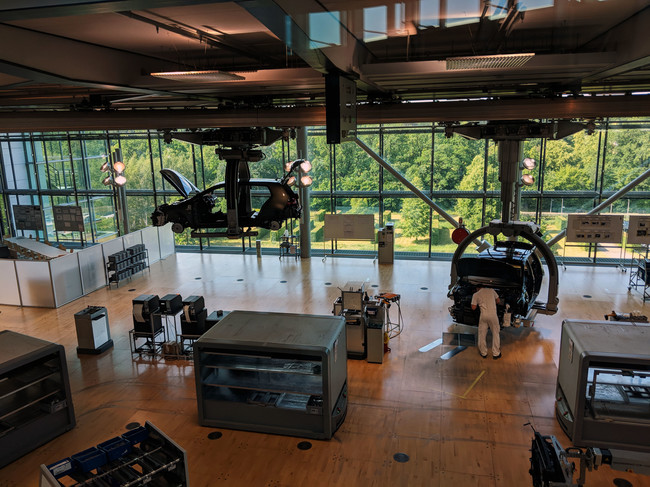
Entre escándalos de emisiones, coches autónomos y car sharing, la industria del autómovil está cambiando mucho en los últimos años. Y la premisa es clara: quien no se adapte está fuera.
Pero claro, es difícil conseguir un equilibrio entre innovar y seguir produciendo lo que demanda actualmente el mercado. ¿Alguien se atrevería a probar un nuevo método de fabricación con ciertos riesgos en su gran planta de producción? Probablemente no.
Por eso mismo, Volkswagen decidió convertir la fábrica en la que hacían coches míticos como el Phaeton o el Bentley Flying Spur en un pequeño (y bonito) laboratorio de experimentos. Así fue nuestra visita a la Factoría de Cristal de Volkswagen en Dresde (Alemania).
El pájaro es la clave
Lo primero que llama la atención al llegar a la planta, además de que parece más un edificio de Calatrava que una fábrica de coches, es su entorno.
Hay más de 350 árboles plantados, un pequeño lago que rodea al edificio y una paz y un silencio que se rompen de vez en con el sonido de pájaros. ¿Pájaros y un edificio de 27.500 metros cuadrados de cristal transparente? No parece una buena combinación.
Para nuestra sorpresa, resulta que el trino de los pájaros que escuchamos es completamente artificial. Bueno, en realidad son grabaciones de pájaros reales que suenan a través de un sistema de bocinas y altavoces repartidos por todo el recinto de la planta.
Según Volkswagen, un equipo de etólogos recomendó este método para evitar que las aves se chocaran contra el edificio. Al parecer, los pájaros no acuden a zonas que consideran ya ocupadas, por lo que, si hay "bullicio aviar", no hay riesgo de choque. Y nos confirman que desde 2016 no ha habido ningún incidente. Al menos durante nuestra visita no vimos ningún pájaro sobrevolando los alrededores. Curioso.
Este pequeño detalle es una muestra del espíritu eco friendly que tiene la Factoría de Cristal. Hay más, como el de las farolas que alumbran el exterior del edificio. Utilizan vapor de sodio y emiten luz de un amarillo que, al parecer, no molesta a los insectos que viven en los Jardines Botánicos que están justo al lado.
O un hecho del que se enorgullecen: ya es una planta carbono neutral en el consumo de energía gracias al uso de renovables. Además, nos confirman que están trabajando para ser también carbono neutral con el consumo de agua. En total, y según sus datos, ahora mismo la fábrica ahorra unas 3.600 toneladas de dióxido de carbono al año.
Pon un tranvía en tu vida fábrica
Además del entorno zen y el cuidado por el medio ambiente, la ciudad de Dresde facilitó la construcción de una línea propia de tranvía para Volkswagen para que se pudieran transportar los materiales y componentes necesarios para la fabricación de los coches.
De esta manera, no tiene que haber camiones entrando y saliendo constantemente hacia y desde la planta, por lo que se evitan atascos y, en consecuencia, hay menos contaminación.
Lo llamaron CarGoTram y circula una vez cada hora desde el almacén de Volkswagen en el distrito de Friedrichstadt en Dresde hasta la propia factoría. Tiene la capacidad equivalente a tres camiones, aproximadamente unos 214 metros cúbicos, y cambia su ruta por la ciudad dependiendo del estado del tráfico. Usa las mismas vías que el tranvía de pasajeros que circula por Dresde.
Se hacen 72 Golfs eléctricos al día (con mucha calma)
La de Dresde es una fábrica muy pequeña. Sólo produce un modelo de vehículo, el Golf eléctrico o e-Golf, y en una cantidad muy discreta: 72 unidades al día. Para hacernos una idea, la fábrica más grande del grupo Volkswagen se encuentra en Wolfsburgo (Alemania) y de sus líneas de producción salen casi 4.000 coches al día.
En esta Factoría de Cristal todo va más lento. Los empleados tienen doce minutos para completar cada tarea, mientras que, según nos aseguran, lo normal es que sean unos tres minutos. Ese tiempo se controla en todo momento con un reloj que se sitúa en el techo. Marca la hora y el tiempo restante antes de pasar a la siguiente tarea:
En cualquier caso, los trabajadores, que se reparten en dos turnos (desde las 6 am y hasta las 10 pm), no parecen nada estresados y están acostumbrados a recibir visitas. De hecho, la fábrica es, al mismo tiempo, una especie de museo al que vienen unas 400 personas al día.
Al contrario que en otras fábricas, donde se limita mucho el acceso tanto por una cuestión de privacidad y el mundo de las patentes como por no molestar ni alterar la producción, aquí puedes entrar y ponerte casi al lado del trabajador que está atornillando cualquier componente del coche.
Como es lógico, esto es posible porque la Factoría de Cristal es básicamente una planta de ensamblaje más que de fabricación. Hay partes del proceso de hacer un coche muy delicadas, como la de pintura, en la que cualquier partícula en el ambiente puede fastidiar el acabado final. Y para entrar a esta planta no hay que pasar ningún tipo de control específico más allá del rutinario de seguridad. En otras fábricas, por ejemplo, te obligan a ponerte unos zapatos de goma para evitar la electricidad estática, bata e incluso un gorro para que no contamines el ambiente.
Una de las cosas que nos llamó la atención es que los propios trabajadores hacen énfasis en que esto no es una fábrica, sino una "manufactura". De hecho, el nombre real de la planta es Gläserne Manufaktur, que literalmente se traduce del alemán como "Manufactura Transparente". "Fábrica" para ellos equivale a producción en serie e industrial, pero "Manufactura" implica trabajo de humanos, y por tanto, algo más de artesanía que de fabricación.
¿En tiempos de automatización y robots hay quien sigue recalcando el trabajo de humanos? Pues sí, pero eso no quiere decir que los 380 empleados de la planta no tengan que recurrir a ellos para determinadas tareas. Por ejemplo, para montar el panel de instrumentos, que pesa unos 60 kilos. O para transportar todos los componentes de un lado a otro, que es una tarea reservada para "cajas" que se mueven solas siguiendo el camino marcado en el suelo.
O para uno de los momentos más llamativos de ver: el matrimonio. Así es como conocen internamente a la unión del chásis con la carrocería. El chásis se coloca en la parte de arriba y se junta con la carrocería en lo que podría ser perfectamente una escena erótica, al menos en el universo de los coches, claro.
Por otro lado, como aquí sólo se fabrican coches que ya están vendidos, los empleados escanean la etiqueta que tiene cada Golf para saber qué elementos tienen que instalar, y es que cada cliente pide los extras y componentes que quiere. Esta personalización es otro de los elementos que utilizan para justificar que haya mano de obra humana para atender a los detalles.
Como curiosidad, la batería que monta este Golf eléctrico pesa 300 kilos y muchos de sus componentes son fabricados por Samsung. Éste es su aspecto:
El último paso en la fabricación del coche viene con el control de calidad, que se hace manualmente en túnel bien iluminado. Aquí los empleados revisan uno por uno detalles como la separación entre componentes, alineación de las diversas partes o imperfecciones en la pintura.
Una vez que atraviesan el túnel, van directamente a sus dueños. Es curioso porque, según nos contaron, en Alemania es costumbre venir a la propia fábrica a recoger el vehículo y que los ingenieros "te lo presenten". Las familias organizan escapadas y planes turísticos para aprovechar que vienen a por su coche nuevo.
Y, claro, Volkswagen no se lo ha pensado para facilitar packs que incluyen entradas para la ópera, tours por la ciudad, e incluso están preparando una especie de showroom para montarte un espectáculo con la música que tú elijas, luces, etc. Como un Salón de Ginebra pero para el coche que te acabas de comprar. Estos packs tienen precios que van desde los 80 a los 400 euros (aparte del coche).
Un futuro eléctrico
Durante la visita, Volkswagen nos reconoció que se está usando esta planta como laboratorio de experimentos.
Por ejemplo, nos contaron que están instalando unos robots que, en teoría, van a mejorar la eficiencia en la producción. La demanda de los e-Golf está siendo alta (en Noruega, por ejemplo, fue el coche más vendido en todos los segmentos en 2017) y ahora mismo en Alemania producen sólo 160 Golfs eléctricos al día entre esta fábrica y otra que tienen al sur, por lo que aumentar la producción es una prioridad total.
El objetivo es que esta planta de Dresde llegue a los 120 Golfs eléctricos al día, y por ello están probando con nuevos robots que prometen mejorar la eficiencia del proceso. Si todo sale bien, nos confiesan, se implementarán también en las fábricas más grandes.
Mario Blank, responsable de logística de la Factoría de Cristal y el segundo al mando de la planta, nos reconoció que son conscientes de que en el futuro desaparecerán puestos de empleo de las fábricas tradicionales y que los robots serán los sustitutos. Sin embargo, al mismo tiempo cree que surgirán nuevos empleos relacionados con la programación y software por lo que, en sus palabras, "la balanza entre los puestos ganados y los que se perderán estará más equilibrada".
Por otro lado, cree que el futuro es completamente eléctrico y nos da una pista: en esta fábrica se hará uno de los nuevos modelos de la familia I.D que se empezarán a comercializar a partir de 2020.
En Xataka | No tan rápido: por qué la revolución de los vehículos eléctricos traerá sus propios problemas consigo
Ver todos los comentarios en https://www.xataka.com
VER 12 Comentarios