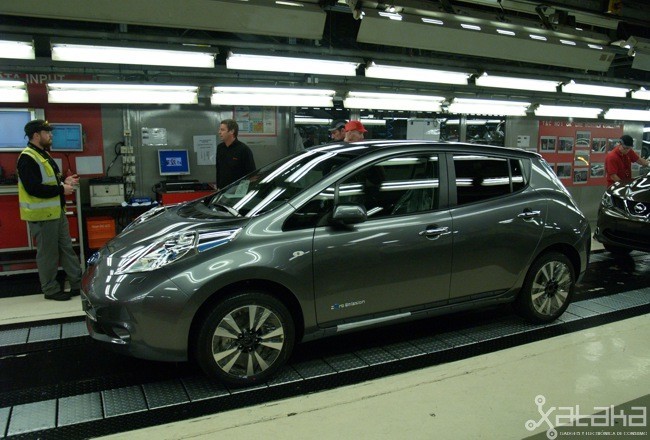
No es la primera vez que hablamos del Nissan LEAF en Xataka. Es uno de los primeros coches eléctricos de la actual generación que se pusieron a la venta, a finales de 2010, y es el coche eléctrico moderno más vendido a nivel mundial. Ya van alrededor de las 160.000 unidades vendidas.
El Nissan LEAF del 2010 comenzó fabricándose solo en Japón, pero ahora se fabrica también en Estados Unidos y en Europa. Nissan nos invitó a visitar la factoría de Sunderland, en el Reino Unido, donde se fabrican varios modelos de coches de esta marca, y entre ellos también el Nissan LEAF 2013 para el mercado europeo. Además también se fabrican baterías para coches eléctricos allí.
En Nissan Sunderland se fabrican 4 coches diferentes
La factoría de Nissan en Sunderland en la más importante de la marca japonesa en Europa, y es una de las más grandes también a nivel mundial. Se inauguró en 1986. En ella se fabrican modelos muy conocidos de esta marca como el Nissan Qashqai o el Nissan Juke, además del Nissan Note y del Nissan LEAF.
En esta planta se construye un coche completamente, desde cero. En Sunderland se producen aproximadamente 120 coches por hora (sí, sí, 120 cada hora, del orden de un coche cada minuto por cada línea de producción, y hay dos).
Nissan aplica un sistema de fabricación integrado en el que puede fabricar componentes y montar diferentes modelos de coche en la misma fábrica y en la misma cadena de montaje. De todos modos el modelo que nos interesa es el enchufable y 100% eléctrico Nissan LEAF.
Esas moles del fondo son las prensas hidráulicas que estampan las piezas de la carrocería
Todo comienza con un rollo de chapa plana
Todo comienza con un rollo de chapa plana. Llega así desde una acería. Estamos hablando de chapa de acero de unos milímetros de espesor. La chapa es el componente fundamental de un coche moderno y el que permitirá construir la carrocería autoportante del automóvil. En según qué coches algunos elementos pueden ser de fundición de acero y otros de perfiles tubulares (extrusión), pero en general la mayor parte es chapa. Otros materiales como el aluminio se utilizan todavía poco en la fabricación de carrocerías, salvo en modelos un poco más especiales (y normalmente más caros).
Pero claro, la chapa por sí sola no sirve de mucho, hay que darle forma. Comenzamos en la sección de conformado donde las prensas hidráulicas van a estampar las diferentes piezas de la carrocería. Es una nave muy diáfana y de gran altura, donde hace algo de fresco. Dentro se ven varias prensas, una gran máquina de un par de alturas (unos 7 u 8 metros de alto aproximadamente).
Dentro discurre una cinta que transporta la chapa plana de esos rollos, avanza al interior de la prensa, se detiene un instante, desciende rápido la prensa, y corta y da forma tridimensional a la chapa (el relieve) mediante la presión que ejerce, para salir la pieza por el otro extremo ya con la forma requerida. Justo en el momento de la estampación se nota un temblor en el suelo, de la gran fuerza que se realiza.
Esa es la cadena de fabricación de la prensa hidráulica que conforma la chapa
El principio básico de la estampación de la chapa es que al plegarla y darle forma "de C", esa misma chapa de pronto gana inercia, rigidez y resistencia para soportar una solicitación, que como chapa plana no soportaría.
Pensad en un trozo de chapa plana rectangular de unos milímetros y ponedla en horizontal: se doblará con cierta facilidad como se dobla una cartulina. Ahora pensad en un perfil con sección en forma "de C" de esa misma chapa, y ponedlo en horizontal: ya no se dobla. Si fuera una cartulina pensad que hacéis un prisma o una cajita con ella, ¿a que ya no se dobla como se doblaba la cartulina inicial?
Obviamente esto es una simplifación, ya que las prensas de conformado para un automóvil fabrican cientos de piezas diferentes con formas tanto más complejas, pero que en esencia responden a este principo "de la C". Todas estas piezas se van almacenando ordenadas para estar a disposición de la siguiente etapa.
Esa pieza de chapa de acero ya conformada, es el lateral derecho de la carrocería de un Nissan LEAF
Un mecano de acero
Todas las piezas de acero estampado son como las de un mecano que hay que juntar, unir unas con otras y montar, para ir construyendo la carrocería del coche. Al ir uniendo unas piezas con otras se va a su vez consiguiendo más rigidez y resistencia, al ir engrosando las secciones, y al arriostrar unos elementos con otros, formando esa gran caja que será carrocería.
La unión de todas las piezas de acero se suele realizar mediante soldadura, y la más habitual es la soldadura eléctrica por puntos. De todos modos en algunos momentos, depende del coche, se puede utilizar otra soldadura con aporte de material, remaches o adhesivos especiales. Salvo algunas piezas concretas que son soldadas por un operario, la mayor parte de las soldaduras las realizan brazos robóticos programados para realizarlas siempre igual y de manera precisa.
En determinados momentos interviene algún operario para colocar una pieza o retirarla, pero en general la mayor parte del proceso está automatizada y los brazos robóticos van cogiendo, moviendo, ensamblando y soldando las diferentes piezas para ir construyendo la carrocería, de manera rítmica y acompasada, como si se tratara de un ballet.
Se comienza por la plataforma inferior y se van levantando los laterales, la parte frontal, el techo, las puertas... Se utilizan plantillas y bastidores para posicionar correctamente unas piezas con otras. Esta parte de la factoría es bastante ruidosa y se ven saltar chispas de la soldadura eléctrica de vez en cuando.
Todas las medidas se controlan mediante máquinas de medición mediante láser que tienen programada una rutina de comprobación de cotas en diferentes puntos de la carrocería, para verificar que todo está donde tiene que estar.
Cuando se termina de construir la carrocería un trabajador suele verificar visualmente y al tacto que las diferentes partes están correctamente, que están ajustadas, que no hay desperfectos, etc (un control de calidad más exahustivo se suele hacer cada determinado número de unidades).
Lo quiero rojo... no, mejor gris
Una vez que la carrocería está terminada llega el turno de la siguiente sección, la pintura. Durante la visita a la planta de Sunderland no pudimos ver el proceso de pintado. Está también automatizado, y habrá que describirlo sin más e imaginárselo, o bien ver algún vídeo de los que hay en YouTube de fábricas muy similares.
Lo más que pudimos ver es cómo entraban carrocerías ya terminadas, listas para pintar, y cómo salían carrocerías recién pintadas, relucientes y bonitas, con el color deseado. Esta sección la atravesamos por un pasillo superior por el que van pasando uno detrás de otro los coches ya pintados, suspendidos de un par de brazos que los sujetan. En esta parte de la factoría hace más calor y se nota un olor un poco más fuerte, similiar a un disolvente suave, que proviene de la pintura.
El proceso de pintado de una carrocería comienza con el lavado de la misma con agua para eliminar restos de grasa y suciedad. Primero se aplica la protección contra la corrosión del acero, hoy en día mediante galvanizado en un baño de zinc.
La siguiente etapa es la inmersión de la misma en el baño cataforético, donde se recubre la carrocería con una capa que también protege contra la oxidación. Después se siguen dando capas, una de imprimación, otra de color, una de laca... el número de capas depende del color y tipo de pintura. Todas se aplican mediante brazos robóticos.
Y ahora a montar todo lo demás
Al final, cuando la pintura de la carrocería está bien seca, puede pasar a la última etapa de la fabricación de un coche, la cadena de montaje de todos los demás componentes y elementos. Estos no tienen porqué fabricarse en esta factoría.
Una parte de esta sección es un almacén en el que se organizan los diferentes componentes que se van a utilizar. Este área es un poco más silenciosa y tranquila, pero la cadena de montaje en sí vuelve a ser un lugar un poco más ruidoso.
Los motores suelen fabricarse en una sección específica, las transmisiones y cajas de cambio también, así como muchas piezas de plástico, como los paragolpes, pero la mayor parte vienen de otras fábricas, o bien del propio fabricante del coche, o normalmente de suministradores especializados en tal o cual producto, que se encargan de fabricar los frenos, los amortiguadores, los cristales, los asientos, los faros, los neumáticos...
Las carrocerías ya pintadas van avanzando despacio, sin prisa, pero sin pausa, por la cadena donde en cada estación trabajadores especializados en tal o cual trabajo van montando este o aquel componente, añadiendo uno después de otro.
Una de las partes más importantes es el encuentro entre la carrocería, con muchos elementos ya montados, y el chasis, que incluye los ejes, con los frenos y amortiguadores, así como el motor y otros elementos del sistema de tracción. La carrocería se cuelga elevada, el chasis se incorpora por debajo, se eleva el chasis hacia la carrocería y se ensamblan.
En un coche eléctrico como el Nissan LEAF, tan importante como esta unión de la carrocería con el chasis, es la unión de la carrocería con la batería, que también se incorpora por debajo y se eleva hasta encajar en su hueco, para atornillarla y conectarla. La fabricación de la batería también se hace en esta factoría de Sunderland, pero en otro edificio.
Esas son las baterías en la cadena de montaje, esperando a que llegue un Nissan LEAF
La batería del Nissan LEAF se fabrica desde cero
La batería del Nissan LEAF que se monta en Sunderland no viene de otra factoría ni de un proveedor, se hace desde cero aquí mismo. Nissan decidió en el año 2006 que fabricaría sus propias baterías para coches eléctricos. Esto supuso una inversión de unos 4.000 millones de dólares, unos 3.250 millones de euros al cambio.
A la planta de fabricación de baterías de Sunderland llegan bobinas con el cátodo y bobinas con el ánodo, que servirán para producir las celdas de la batería. Estas bobinas son fabricadas en Japón por una empresa conjunta participada por Nissan y por NEC. Visualmente son una lámina de plástico de color casi negro que contiene las moléculas del compuesto del ánodo y del compuesto del cátodo. Cada bobina tiene unos 2 km de largo y da para fabricar las celdas necesarias para las baterías de siete Nissan LEAF.
Primero tiene lugar la laminación de las celdas
Desde que entran dentro del edificio de fabricación de las celdas, todo cambia. Este edificio es de acceso restringido, su atmósfera está controlada, para que la calidad del aire sea siempre la adecuada, para que la temperatura sea prácticamente constante, así como el grado de humedad ambiente, para que sea muy bajo, y sobre todo, para que el ambiente esté muy limpio.
Para poder acceder a este edificio "limpio", hay que vestirse adecuadamente. Hay que quitarse los zapatos de la calle y ponerse unos "limpios", y hay que ponerse un mono completo de material sintético, una capucha, unos guantes y una mascarilla, para evitar contaminar y ensuciar el ambiente interior.
Hay que tener en cuenta que el polvo, ya sea de la tierra que puedan llevar unos zapatos, de las fibras y pelusas que puedan desprender las prendas de ropa, o incluso nuestra propia piel o cabellos, pueden contaminar el ambiente interior y echar a perder la fabricación de las celdas. La humedad o el polvo, pueden provocar malos contactos y cortocircuitos en el interior de la propia celda, de ahí que haya que tener tanto cuidado.
Esas son las bobinas con el ánodo y las bobinas con el cátodo
Después de vestirnos adecuadamente, hay que pasar por una cámara de ducha de aire con chorros de aire que "nos soplan", para retirar las pocas partículas de polvo que podamos todavía llevar encima. En el suelo unas láminas de plástico pegajosas retiran también cualquier pequeña partícula que pudieran llevar las suelas de los zapatos.
Dentro, el proceso está casi por completo automatizado. Los trabajadores tienen que cargar las bobinas de cátodo y ánodo, así como de otros elementos, las membranas de plástico que hacen de separadores entre uno y otro, o la lámina de plástico que envuelve cada celda.
Conviene recordar en este momento que la batería del Nissan LEAF es de iones de litio y manganeso con celdas de tipo laminar. Cada celda viene a ser como un sobre de tamaño folio dentro del cual hay varios folios superpuestos (lámina de ánodo, lámina de separador, lámina de cátodo), y finalmente el sobre está relleno con el líquido electrolito.
La bobina con el ánodo y la bobina con el cátodo comienzan en la etapa de encintado, donde se le añade una cinta de aluminio transversal cada cierta distancia. A continuación cada bobina se corta longitudinalmente en tres bandas, de modo que cada bobina al final serán tres, pero más estrechas.
Esas son las celdas llenas de electrolito
De ahí se pasa a una máquina de laminación que va a juntar la lámina de ánodo, con la lámina de cátodo, intercalando la lámina de separador entre ambas (de color blanco). El número exacto de láminas que se superponen de cada uno no nos lo cuentan, pues es "la receta secreta".
El siguiente paso es colocar el plástico exterior de la celda y los bornes positivo y negativo de la celda, que son una pequeñas láminas rectangulares de aluminio una y de cobre la otra.
Las celdas casi terminadas se apilan en bandejas y de ahí pasan a la penúltima etapa de la "sala limpia", donde se inyecta el eletrolito líquido dentro de cada celda (el "sobre" que os decía antes). Las celdas ya con el electrolito tienen que envejecer para que su estructura química se forme correctamente. Se carga eléctricamente cada celda y finalmente se sellan todos los bordes de cada una: ya está lista para salir de esta zona.
Durante todo el proceso de fabricación de las celdas se realizan múltiples controles de calidad, unos automáticos, y otros mediante los técnicos que trabajan allí, tomando muestras para pruebas de laboratorio.
Aquí vemos cuatro celdas apiladas
Después se hacen los módulos
El resto del proceso de fabricación de las baterías ya no requiere de un control tan exhaustivo de la temperatura, humedad y limpieza, y se realiza en una parte de la planta más convencional (aunque no del todo).
Las celdas que salen de la sala limpia se comprueban una por una visualmente por un operario. Todas, sin excepción. Después se rectifican dimensionalmente con una máquina automática que recorta los bordes de plástico sobrantes y comprueba las dimensiones exactas que tienen que tener las celdas.
A continuación se apilan las celdas de cuatro en cuatro, en una estructura de aluminio y plástico, se sueldan los bornes positivo y negativo y se colocan las tapas de aluminio que finalmente dan lugar al módulo de la batería. De nuevo otro operario comprueba visualmente que cada módulo está correcto.
Esto es un módulo de batería del Nissan LEAF ya terminado, con su recubrimiento de aluminio
Finalmente se montan los módulos en el paquete de la batería
Los módulos de batería se pueden guardar en cajas en este punto, por ejemplo para enviarlos a la factoría de Nissan en Barcelona, donde se ensamblan para hacer el paquete de batería para la furgoneta eléctrica Nissan e-NV200 que se fabrica allí, o bien se utilizan directamente en la última sección de la factoría de baterías de Nissan Sunderland, donde se montan en el paquete de la batería del Nissan LEAF.
El montaje del paquete de la batería viene a ser otra pequeña cadena de montaje, donde operarios tienen que ir juntando y ensamblando los modulos dentro de la carcasa de acero del paquete de la batería. Esta carcasa de acero se hizo a partir de chapa de acero que también se conformó en la sección de prensas hidráulicas, que también pasó por un proceso de soldadura para ensamblar varias piezas de acero y también pasó por pintura.
Hay muchas piezas que poner, y todas se ponen a mano: soportes de aluminio, soportes de plástico, tornillos de acero, cableado... Cuando uno piensa en la batería de un coche eléctrico no se para a pensar la cantidad de piezas y de tornillos que realmente lleva dentro, para sujetar cada módulo en su sitio.
La batería se termina cuando se coloca la tapa de acero del paquete de la batería. El paquete queda sellado para que no le entre agua. Una vez terminada se carga por completo. La batería terminada, completa, viene a pesar del orden de los 294 kg.
Estos paquetes de batería son los que pasan a la cadena de montaje del coche para añadirlos a la carrocería, tal y como os contamos antes. Cada uno lleva 48 módulos, y cada módulo 4 celdas, es decir, que en total cada coche lleva 192 celdas. La fabricación de un paquete de batería del Nissan LEAF ha llevado desde el principio, desde la fabricación de las bobinas de cátodo y de ánodo, hasta el final, más de 2.000 controles de calidad.
Sinceramente, después de conocer al detalle todos los procesos mecanizados, todos los trabajos a mano que hay que realizar, todas las piezas que hay que montar y todos los controles de calidad que se realizan, comprendo y entiendo que la batería de un coche eléctrico sea a día de hoy todavía tan cara. Por cierto, Nissan anunció hace unos días que en España, la batería de sustitución del Nissan LEAF costará 6.050 euros, cuando llegue el momento de cambiarla, y esté fuera del período de garantía.
Y se acabó: ya tenemos un Nissan LEAF nuevo
Cuando la carrocería ya tiene todos los componentes montados pasamos por fin a tener un coche. Este sale de la cadena de montaje y pasa el control de calidad, donde se revisan varios parámetros por un operario, como el aspecto general del coche, que las puertas abren y cierran bien, que el motor arranca, que los limpiaparabrisas funcionan o las luces se encienden, entre otras cosas.
Comprobado todo, el Nissan LEAF está listo para esperar a ser llevado hasta su destino, un concesionario o bien un cliente que está esperando por él.
Los gastos del viaje para asistir a esta visita han sido asumidos por la marca. Para más información consulta nuestra política de relaciones con empresas.
Vídeo | Adriano (Nissan - YouTube)
En Xataka | ¿Qué puede ofrecer un coche eléctrico como el Nissan LEAF a una gran ciudad como Londres?
Ver todos los comentarios en https://www.xataka.com
VER 14 Comentarios