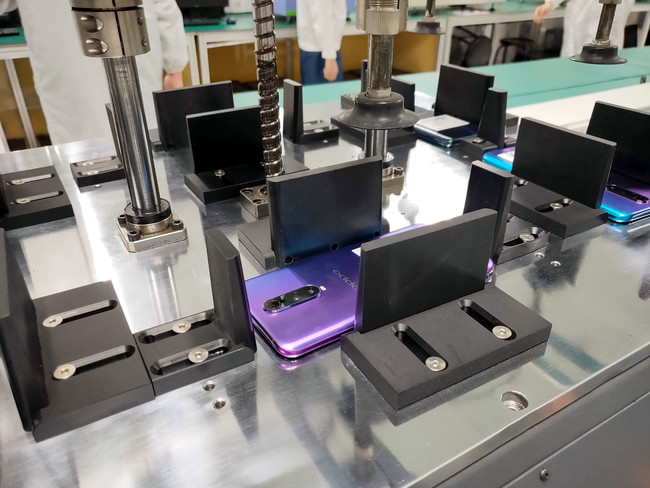
OPPO desembarcó en Europa el pasado mes de junio con un evento por todo lo alto en el que anunciaron el OPPO Find X, su actual buque insignia. La compañía china era prácticamente desconocida en el viejo continente a pesar de que en 2016 ya se había colado en el top 5 de fabricantes a nivel mundial. En su día ya hablamos acerca de OPPO, sus inicios y filosofía, y recientemente hemos tenido la oportunidad de conocerla "en persona".
OPPO fue fundada en Dongguan, China, ciudad donde se encuentra la sede de la compañía y una de sus seis fábricas también denominada 'campus'. El campus de OPPO en Dongguan no es sólo una fábrica, sino más bien una miniciudad. Además de las líneas de producción y montaje, también tiene zonas de recreo, guarderías, restaurantes y mucho más. Así es la fábrica de OPPO por dentro.
La fábrica de OPPO en vídeo
Los números de OPPO
Antes de entrar en harina veamos algunos datos acerca de OPPO, empezando por su posición en el mercado, tanto local como global. Según los últimos datos de Counterpoint, en China, OPPO es el tercer fabricante por detrás de Huawei y Vivo, con quien empató con un 21% de cuota de mercado en el tercer trimestre de este año.
Si miramos la foto completa, a nivel mundial OPPO se encuentra en el quinto puesto del ranking con un 9% de cuota de mercado, también según Counterpoint. A principios de 2017, OPPO llegó a estar en el cuarto puesto según datos de IDC, pero antes de acabar el año fueron adelantados por Xiaomi, otro fabricante chino que también comenzó su internacionalización hace poco. Actualmente, OPPO está presente en 31 países, la mayoría de ellos en Asia y, desde el pasado verano, también algunos europeos.
Con respecto a las fábricas, OPPO cuenta con nueve plantas de producción, seis de ellas en China y las otras tres en Indonesia, India y Argelia. Nosotros visitamos una de las plantas en China, la de Dongguan, que además también es uno de los seis centros de I+D que tienen en todo el mundo. Y ahora sí, veamos cómo es el campus de OPPO en Dongguan.
Primera parada: laboratorio de calidad
La primera parte de la visita transcurrió en el departamento de control de calidad, donde se ponen a prueba los dispositivos para ver como responden ante distintas situaciones. Dicho de otro modo, es donde los móviles son sometidos a todo tipo de 'torturas'.
Cada modelo pasa más de 150 pruebas que se dividen en tres bloques: pruebas de rendimiento eléctrico, pruebas estructurales y pruebas de envejecimiento ambiental.
Las caídas son uno de los peligros más habituales a los que se enfrentan nuestros smartphones y OPPO dedica una buena parte de su laboratorio a probar la resistencia de sus productos. En el GIF sobre estas líneas podemos ver el test de "microcaídas", en el que se pretende simular golpes suaves, como por ejemplo al dejar el móvil sobre una mesa sin mucho cuidado.
Esta prueba tiene distintas variantes dependiendo de si el móvil cae con la pantalla, con la trasera o con los laterales. La altura es de 7 centímetros y el número de repeticiones total es de 42.000 por dispositivo.
También hay un test de caídas más fuertes en el que el dispositivo es dejado caer, primero desde una altura mínima de 1 metro. Si no sufre daños se hace un segundo test donde la altura se aumenta a 1,5 metros. En este caso también se repite la prueba desde todos los lados del terminal, tanto pantalla y trasera como todos sus laterales y esquinas.
Esta prueba es bastante más violenta ya que la máquina que eleva el terminal no solo lo deja caer, sino que lo empuja contra el suelo de forma que el impacto es bastante fuerte. También se prueba la flexibilidad del terminal con un test de torsión.
Otro de los problemas a los que se enfrenta un dispositivo como un teléfono móvil es el uso continuado. En el laboratorio también se realizan pruebas para determinar el aguante de ciertos componentes. Por ejemplo el mecanismo deslizante del OPPO Find X se acciona sin parar para ver su grado de resistencia. Según OPPO, aguantará hasta 300.000 repeticiones sin romperse.
Con los botones físicos también se hacen pruebas de resistencia para ver cuántas pulsaciones soporta antes de fallar. Concretamente se hacen 100.000 pulsaciones con una presión de 1 kilogramo. Si pulsamos los botones 50 veces al día, para alcanzar esa cifra tendríamos que esperar seis años.
Hay más test de desgaste como el que conecta el cable USB-C repetidamente o el que prueba el aguante del cable a torsiones continuadas con peso en un extremo.
Por último, vimos varias máquinas destinadas a pruebas en las que se simula la respuesta a agentes externos como temperaturas extremas, humedad, polvo y agua. Para probar la resistencia al agua, se colocan los dispositivos dentro de una cámara y se simula lluvia. Después se comprueba que todas las funciones son normales y se abre el dispositivo para descartar corrosión en los componentes internos.
En esta área también se hacen pruebas con agua salada y un líquido que simula sudor. En esta prueba concreto, se envuelve el dispositivo en un trapo empapado en este sudor artificial y se coloca en una cámara con alta temperatura y humedad donde pasa al menos dos días.
Segunda parada: línea de montaje
Tras asistir a todas las sesiones de tortura descritas, nos dirigimos a una de las 26 líneas de montaje con las que cuenta la fábrica. Concretamente, estuvimos en una de las líneas donde se estaba ensamblando el OPPO R17, modelo que llegó a Europa el pasado mes de noviembre como OPPO RX17 Neo.
En esta parte de la fábrica hay distintos puestos donde se van ensamblando las principales piezas, tanto mediante máquinas automatizadas como de forma manual por empleados. Por ejemplo, la carcasa trasera es colocada por un empleado pero después pasa a una especie de prensa donde se asegura que la pieza quede bien pegada a la trasera.
Durante el proceso los operarios realizan muchas comprobaciones oculares, como sucede con la cámara donde dos empleadas miraban detenidamente que la app funcionara bien y comparaban dos modelos al azar en busca de desviaciones de color u otros fallos.
Hablando de los empleados, hubo un detalle que llamó la atención en la visita y es que en China es costumbre hacer descansos en el propio puesto de trabajo. Los responsables de OPPO nos indicaron que debido a la naturaleza repetitiva del trabajo en la línea de montaje, es habitual que los empleados hagan pausas en las que algunos aprovechan para echar una cabezadita apoyados sobre la mesa.
En esta parte de la visita también nos dirigimos a la zona donde se realiza todo el trabajo de circuitería o PCB. Lo más curioso es que para entrar en esta área primero nos hicieron pasar por una especie de ducha de aire para quitarnos posibles partículas de polvo que lleváramos adheridas a la ropa. El motivo es que se trabaja con componentes diminutos y cualquier contaminante podría causar problemas en la impresión de los circuitos.
Como decía, en total hay 26 líneas de producción y montaje en esta fábrica. Sólo esta planta cuenta con una capacidad para producir nada menos que 311 móviles por minuto, más de 18.600 móviles por hora. Casi nada.
Tercera parada: un paseo por el campus
Pero la fábrica de OPPO en Dongguan es más que una simple fábrica. Muchos de los empleados viven dentro del área denominada campus, donde cuentan con instalaciones de todo tipo que lo convierten casi en un pueblo dentro de la ciudad, y no uno pequeño. No nos precisaron una cifra exacta pero en la planta trabajan entre 15.000 y 20.000 empleados, que se dice pronto.
Al acabar nuestra visita a las instalaciones fuimos a comer al restaurante Ollie, el único sitio para comer a la carta. La gran mayoría de empleados come en una de las cantinas donde se sirven distintos menús y los precios son más ajustados. En total, hay 7.000 metros cuadrados de superficie destinada a la alimentación donde hasta 2.000 empleados pueden comer de forma simultánea.
Después de comer visitamos algunas zonas de recreo, incluyendo un parque infantil para los empleados con hijos pequeños y una sala con máquinas recreativas y billares. Además, nos indicaron que hay librerías, gimnasios y superficies deportivas como canchas de basket, badminton y hasta un campo de fútbol. Por cierto, curioso que en el campus los miércoles por la tarde como día de ejercicio para los empleados.
También hay siete edificios de dormitorios para empleados que viven dentro del campus, porque no todos se alojan en el interior, también los hay que viven en la ciudad de Dongguan que cuenta con más de ocho millones de habitantes.
Nuestra visita concluyó en uno de los edificios de oficinas donde asistimos a un workshop sobre Super VOOC, el sistema de carga rápida de la marca. No pudimos verlo todo pero en el tiempo que estuvimos fue suficiente para hacernos una idea de la magnitud de esta fábrica y, sobre todo, la miniciudad que la rodea.
Ver todos los comentarios en https://www.xataka.com
VER 9 Comentarios